Roto Ups the Pace of Digitalization
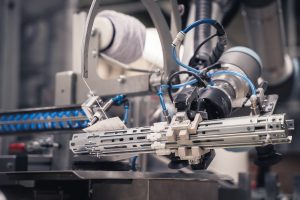
By using collaborative robots, Roto Fenster- und Türtechnologie (FTT) is taking the next step in digitalizing production. The new technology which has been tried and tested in the Hungarian town of Lövő automates the packaging of finished hardware parts. Plans are in place to roll it out in the construction supplier’s other 15 factories around the world. This improves the delivery quality for customers. Photo: Roto / Máté Csoba
Leinfelden-Echterdingen – Digitalization in production is not an end in itself but must always lead to tangible improvements for the company and its customers. Keeping this in mind, Roto Fenster- und Türtechnologie (FTT) reports on further targeted Industry 4.0 projects. After recently announcing its entry into additive manufacturing, the globally active hardware manufacturer is now detailing the integration of collaborative robots in its production processes. In addition, Roto FTT will soon take its next step in digitalization with online machine diagnostics.
A collaborative robot can work in the same area as people, right next to them, and in the event of a possible collision, it automatically reduces the speed to a stop, explains Dr Stefan Thiemermann. According to the FTT Production Director, complex protective fencing is therefore unnecessary. After intensive analysis and preparations, Roto began the testing of the first robot halfway through 2020. It was installed on the automatic packaging unit at a rotary table workstation for center lock assembly in the Hungarian town of Lövő. This “new member of staff” is tasked with stacking the components transported by a conveyor belt, then bundling and labelling them before placing them in a container.
The test period is now complete and normal operation using the robot has begun. The extensive practical experience of using this technology that has been collected and evaluated was used as an important parameter for the exact specifications of the next similar robot. It is also used to package finished parts for use. To this end, it is directly allocated to an automatic stay guide assembly station which produces, for example, “Roto NX” hardware in large quantities and in two different lengths.
The aim is to add a driverless transport system to this collaborative duo at a later point at the location in Lövő. Ernö Kocsis explains that this digitalization technology is intended to automatically replenish long semi-finished parts both between the warehouse and the relevant automatic machines as well as between the packaging cell and the finished parts warehouse. Hopefully, this eliminates waiting times and speeds up production processes throughout different stages of the process
For the window and door technology specialist’s customers, the new age of robots, which is to be rolled out to the other 15 FTT factories around the world, will have a positive impact on delivery quality in particular. It will be more efficient, reliable and accurate.
In 2021, the Roto FTT factory in the Hungarian town of Lövő can look back on 25 years of continuous growth. After being modernized and extended numerous times, it is the largest production location in the hardware manufacturer’s global production network. According to Roto FTT, this is another reason why this location offers the “best prerequisites” for implementing new digital pilot projects. Photo: Roto / Máté Csoba
More seamless production
By contrast, a second digitalization pilot project is still in the initial stages of a “ground-breaking development”. This project is dedicated to maintaining the functionality of systems in the long term by collecting and processing technical data using artificial intelligence. In specific terms, this means detecting possible machine malfunctions at an early stage, preventing serious faults, minimizing maintenance costs and avoiding production downtime. Ultimately this would hopefully ensure that customers enjoy the benefits of on-time delivery. This permanently stabilizes the window and door manufacturer’s production processes.
To achieve these aims, Roto is working intensively on online machine diagnostics. Lövő, as the largest production location in FTT’s production network, offers the best prerequisites for this with a good 600 employees. For instance, it features a series of automatic punching presses. The new digital system is being trialed on one of these. Kocsis expects the pilot project to be successfully completed by the start of 2022, with the aim of transforming other factories afterwards.
The current Industry 4.0 examples are a testament to the consistent implementation of the multifaceted digitalization strategy, concludes Thiemermann. The Production Director also highlights the contribution they are making to operational excellence in production and logistics, as well as to tackling the national shortage of staff through further automation.
“Digitalization is a key driver for our vision of operational excellence,” states Dr. Stefan Thiemermann. The Production Director at Roto Fenster- und Türtechnologie (FTT). Dr Thiemermann cites the hardware producer’s new Industry 4.0 projects as evidence of this. Photo: Roto
Ernö Kocsis also believes that systematic digitalization in hardware production is indispensable. The Managing Director of Roto Elzett Certa Kft. in the Hungarian town of Lövő describes the development, testing and implementation of the new “collaborative robot” and “online machine diagnostics” technologies as “important components” of superior production and delivery quality. Photo: Roto
Related Posts

Roto Inside – May 2020
