Roto: 3D printing offers added value for customers
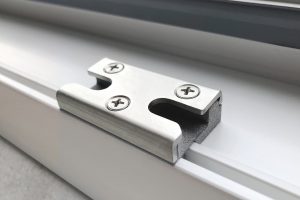
A steel frame locking component with PVC packer
Creating added value for customers, generating growth, boosting efficiency and ensuring sustainability – these core objectives lie at the heart of Roto Window and Door Technology (FTT)’s strategic digitization initiative. According to the company, this is a long-term initiative split into numerous individual projects. Following on from the two solutions already rolled out – “Roto City” and the “Profile database” – the next step in the digitization process will now be implemented: the production of small series based on additive manufacturing technology.
The new process uses existing 3D data to produce PVC components with mechanical properties comparable to those offered by injection molding. Thanks to tool-free production, 3D printing enables fast, flexible customer-focused manufacturing of components in small and very small series. The production range also includes jigs, samples and spare parts, as well as testable high-strength prototypes. The substantially shorter time to market offers tangible benefits to customers and supports them in the digital transformation of their business. This is another example of how Roto is proving to be a forward-looking partner.
We use Multi Jet Fusion technology from HP, which is a powder-based printing process. Unlike the more widely-known SLS printing method, instead of using a laser for the melting process, it uses an infrared lamp to melt the powder material in layers. Heat-absorbing liquids (fusing agents) only fuse certain areas of the powder bed, resulting in sharp outlines and high dimensional accuracy of the printed components. The multi-stage printing process results in a finished component, functional element or complete functional assembly.
Our first international case-study property is already demonstrating the real-life application of the new 3D components. The Alexandra Hospital in Redditch, Worcestershire, England, has been fitted with 1000 Tilt-Only windows. The windows were manufactured by 3D Aluminium, Oxfordshire, using an aluminium system from Hydro Building Systems. In order to meet the delivery schedule, Roto was able to print and supply the right amount of PVC packers for the frame center closers at short notice. This latest project also serves to illustrate the breadth of the window and door technology specialist’s ongoing digitization strategy.
Related Posts

Roto Inside – May 2020
